Common Structural Concrete Issues in DFW and How to Avoid Them
Commercial buildings in the Dallas-Fort Worth (DFW) area rely heavily on durable structural concrete to withstand the region’s challenging climate and high-traffic demands. However, even the most robust concrete structures can face issues over time if not properly maintained. From temperature fluctuations to soil conditions, several factors unique to DFW contribute to concrete wear and tear. Identifying these common issues and taking preventive measures can significantly enhance the structural integrity of commercial properties in Texas. Here’s an overview of the most common structural concrete problems in DFW and practical solutions for avoiding them.
1. Cracking Due to Temperature Fluctuations
One of the most frequent issues affecting structural concrete in DFW is cracking, often caused by extreme temperature changes. The region’s hot summers and cooler winter months lead to concrete expansion and contraction, creating stress that can result in cracks. While minor cracks are common, larger cracks can weaken structural integrity if left untreated.
Preventive Measures:
- Expansion Joints: Installing expansion joints allows the concrete to expand and contract without causing large cracks. Properly placed joints are essential for preventing temperature-related cracking.
- Quality Concrete Mix: High-quality concrete mixes designed for DFW’s climate can minimize the risk of cracking. These mixes often include additives that improve flexibility, allowing the concrete to withstand temperature changes more effectively.
By using appropriate materials and techniques, property owners can reduce temperature-induced cracking and extend the lifespan of their concrete structures.
2. Erosion from Moisture and Rainfall
DFW’s climate also brings seasonal rain, which can lead to moisture-related erosion in concrete structures. When rainwater seeps into cracks or porous surfaces, it can erode the concrete from within, weakening the structure and leading to issues such as spalling and crumbling. Poor drainage around the building exacerbates this problem, allowing water to pool near the foundation.
Preventive Measures:
- Proper Drainage Systems: Installing effective drainage systems, such as French drains or sloping landscapes, prevents water from pooling around concrete structures. This simple step can reduce the risk of water-related erosion.
- Sealing: Applying a waterproof sealant to the surface of the concrete creates a barrier that keeps moisture out. Sealants should be reapplied periodically to maintain their effectiveness, particularly in high-exposure areas.
By managing water flow and protecting concrete surfaces from moisture, property owners in DFW can reduce erosion-related structural issues and maintain the integrity of their buildings.
3. Soil Movement and Foundation Shifting
DFW is known for its expansive clay soil, which can expand and contract significantly based on moisture levels. This soil movement places additional stress on concrete foundations, leading to shifting, settling, and even cracking. As the foundation shifts, the entire structure can experience alignment issues, which may result in cracked walls, uneven floors, and compromised stability.
Preventive Measures:
- Soil Stabilization Techniques: Before construction, soil stabilization methods, such as lime treatment or soil compaction, can improve soil consistency and reduce movement.
- Regular Foundation Inspections: Routine foundation inspections allow property owners to detect early signs of movement, such as hairline cracks or small shifts. Addressing these signs early can prevent more significant structural issues.
Taking proactive steps to stabilize the soil can prevent foundation-related problems and protect the overall structure from the effects of soil movement.
4. Rusting of Reinforced Steel
In reinforced concrete, steel bars (rebar) provide additional strength to support heavy loads. However, when moisture penetrates the concrete, it can cause the steel to rust. As the steel rusts, it expands, putting internal pressure on the surrounding concrete and causing cracks, spalling, or even structural failure over time. This issue, known as “concrete cancer,” is particularly concerning in humid regions like DFW.
Preventive Measures:
- Proper Concrete Cover: Ensuring an adequate layer of concrete covers the rebar minimizes its exposure to moisture. During construction, reinforcing bars should be placed with a sufficient concrete cover to protect against water infiltration.
- Corrosion-Resistant Rebar: Using epoxy-coated or galvanized rebar can reduce the likelihood of rusting, especially in areas exposed to moisture. These corrosion-resistant options may have a higher upfront cost but offer long-term protection against rust-related damage.
Protecting the rebar from moisture is essential to preserving the structural integrity of reinforced concrete in DFW’s climate.
5. Spalling and Scaling from Surface Damage
Spalling (chipping or flaking) and scaling (peeling of the surface layer) often occur when concrete is exposed to repeated freeze-thaw cycles, moisture, or chemical exposure. In DFW, heavy rainfall combined with occasional winter freezes can lead to these types of surface damage, compromising both the appearance and durability of the structure.
Preventive Measures:
- Surface Sealing and Coatings: Applying a protective coating, such as a concrete sealer, can prevent moisture penetration and protect the surface from scaling or spalling. This protective layer also minimizes the impact of freeze-thaw cycles, reducing surface wear.
- Avoiding Deicing Chemicals: In the winter, deicing chemicals can contribute to scaling by accelerating the freeze-thaw cycle and weakening the concrete surface. Opting for non-chemical deicing methods, like sand, can help protect concrete surfaces from this type of damage.
By maintaining the concrete’s surface integrity, property owners can prevent surface damage that could eventually affect the structure’s strength.
6. Inadequate Maintenance and Repair
Finally, one of the most common reasons concrete structures face significant issues is neglecting regular maintenance. Without proper care, minor issues can escalate into costly structural problems. In DFW, where weather extremes are common, a proactive maintenance schedule is crucial for preserving commercial concrete.
Preventive Measures:
- Routine Inspections: Regular inspections can detect early signs of damage, including small cracks, moisture penetration, and surface wear. Addressing these issues early on helps maintain the concrete’s structural integrity.
- Timely Repairs: Quick repairs, such as filling cracks or reapplying sealants, prevent small problems from becoming major concerns. Enlisting the services of experienced concrete professionals ensures repairs are done effectively.
A consistent maintenance plan helps DFW property owners protect their investment and ensures that commercial buildings remain safe, functional, and attractive over time.
Expert Concrete Solutions for You
Contact us today for a consultation or project estimate. We're here to help!
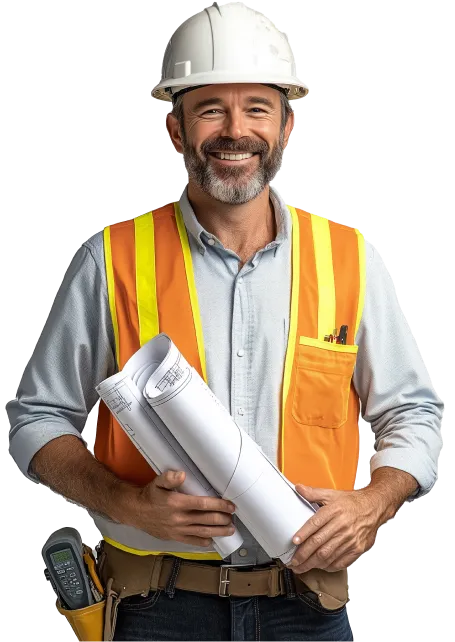